The fabrication process of engravings
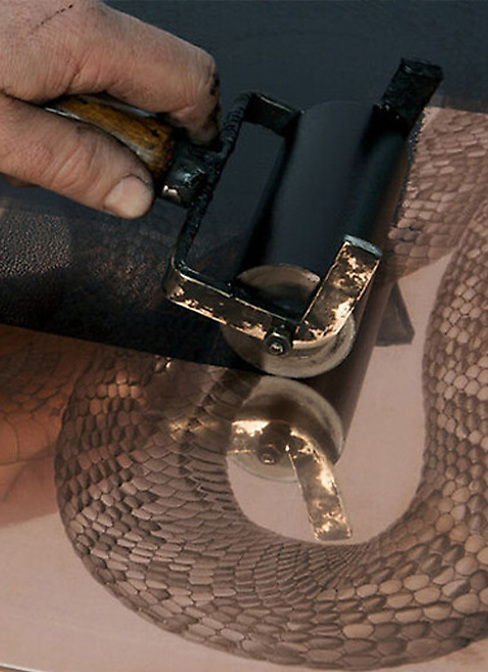
How are engravings made?
Every day, dozens of prints come off the presses of GrandPalaisRmnAteliers. The Louvre's Chalcographie collection comprises over 14,000 print matrices, the oldest of which date back to the 17th century. These are copper plates engraved using the taille-douce technique, in which the motif is recessed into the metal (unlike etching, where the subject is in relief). Burin and etching are the two engraving techniques most represented in the collection, which also includes aquatints, crayon manners, drypoints and heliogravures.
The Louvre's Chalcographie collection also includes around a hundred wood (xylography) and stone (lithography) matrices. For technical reasons, these plates are not used.
Printing intaglio plates
When printing a plate, the printer begins by removing the varnish that protects and preserves it when in storage. After cleaning, he checks that it is in good condition, to ensure a quality print run and avoid damaging the plate. Once this reconnaissance work has been carried out, it's time to print.
The printer first inks the matrix generously: the entire surface of the metal must be covered with a thick ink, made from linseed oil and pigments and specifically designed for intaglio printing. The ink is applied with a roller and then a leather pad. To facilitate this operation, the engraved plate is placed on a heating table to make the ink more elastic. The printer ensures that each size is properly inked.
Wiping: the most important and delicate stage
Using a muslin cloth called tarlatan, the printer removes the excess ink, gradually revealing the design. The unengraved parts are cleaned of ink, which must remain lodged only in the sizes. The printer finishes the operation with the palm of his hand, covered with a little Spanish white, to remove the last unwanted traces of ink. The bare metal should then shine like a mirror. This last operation, called "paumage", requires great dexterity.
Transferring ink to paper
The printer then places the inked plate on the intaglio press platen. He covers it with a sheet of paper, previously moistened to make the fiber more receptive to the ink. The whole is protected by thick felt cloths, which absorb the very high pressure of the machine. In a horizontal movement, the die and paper pass under the press cylinder. The ink is transferred from the die to the paper fiber: it is said to be "in love with paper".
The printer can then remove the sheet and reveal the print. Due to the high pressure exerted on the wet paper, the sheet retains a bowl, which corresponds to the perimeter of the matrix: this is known as the "coup de planche".
The printed proof, still wet, is placed between blotters and thick cardboard. The printer can then ink the plate again, repeating each operation to obtain another print run.
The final stage: checking and applying the dry stamp
After forty-eight hours of drying, each print is meticulously examined to ensure that there are no defects. Prints that do not meet the quality requirements of the art workshops are systematically discarded. Then comes the final stage in the manufacturing process: the application of the Chalcographie du Louvre dry stamp. This embossed mark on the edge of the print certifies the quality and authenticity of the print.